TUG OF WAR
- Sylvain Ubersfeld
- 22 juil. 2017
- 15 min de lecture
The ideal world for any loadmaster working for any cargo airline in any country of the planet would be a world in which all airport handling equipment would be standardized, airport workers would all speak English, landing and parking fees would be charged directly to the company, toilet cleaning services would REALLY empty the toilets and catering would be as tasty as a first class restaurant in France, Germany or Switzerland.
Of course, in an ideal world, crews would always be in a good mood, Jeppesen books would always been updated and ground handling companies would be cheap and reliable. But as we all know the “ideal world” does not exist, and this is a good opportunity to make one’s life a bit more exciting…
Back in the 80’s in South America, things were not at all like they were at home.

(Our shaft was longer, but this is a shaft allright: ours was 76.000 lbs in one piece...)

( I guess it was about "the right size"...looks much more like the one we carried)
I always loved the South American culture and people, something probably coming from a previous life as Peruvian half-god, a Colombian prince , a Bar Manager in Costa Rica (with girls included) or a cocaïne peddler in the streets of Bogota...
Any time the company looked for a devoted loadmaster to cover a flight to South America, I would volunteer, obviously looking for adventure and emotion.
Although I was a defective, inadequate, substandard pupil and student in my early youth, I managed to pick enough Italian to operate in major Italian airports, and enough Spanish to survive short or longer stays in countries where Spanish is the national language, running from Argentina to Mexico and my interest for foreign languages helped me tremendously during the my 43 years in the airline industry and through my three successive aviation employers !
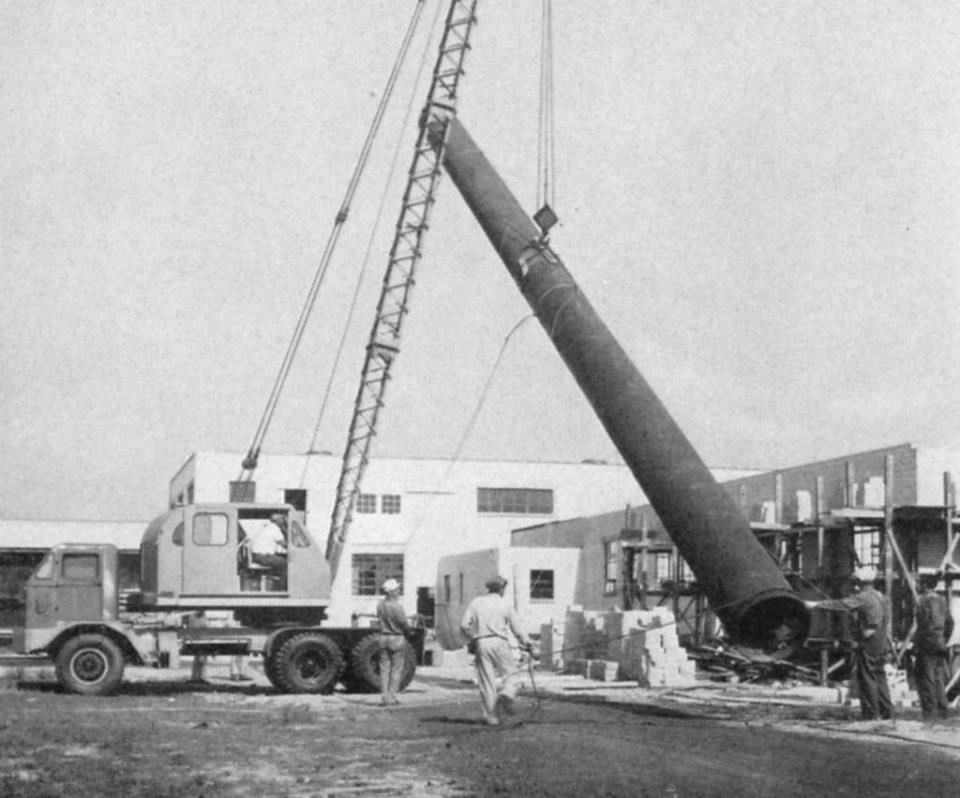
(What our crane looked like...not a very inspiring sight...!)
Miami was an impressive place to be and this was my very first time there ! With a French vision of the US, I was convinced that Miami (or for that matter Florida as a whole) was split into two communities: -an aging Jewish population with whom I would feel perfectly fine and -a more musical one of Cuban origin drinking smart cocktails at the terrace of popular hangouts and cracking mocking jokes about Castro while playing dominoes….
I had forgotten one community : the girls of Florida, everywhere I could look….but I had no time for this ! Up early the day after my arrival , I Joined my crew and my airplane at Miami International, Dade County airport.

(Or was it this model?)

(The "old" airport: no equipment ....brain and balls operation ! Expansion started in 2006, long after my days...)
Sure enough, my load was there. So was a team of crane operators, complete with chains, hooks, talkie-walkie, and on a huge flatbed truck a 70 ft. 76.000 lbs ship crankshaft needed for replacement on a container ship stuck somewhere in the Panama Canal area ! I had never seen such a piece of cargo so big that I could even “feel” the weight of that thing just by looking at it.
Picked up by the crane operators in a very precise operation, the crankshaft was loaded on two 20 ft. cargo pallets equipped with the necessary wooden shoring beams necessary to equally spread the weight of the load due to airplane structural limitation as well PDU ( power Drive Units) constraints. The 20ft pallets had been positioned on two main-deck loader strong enough to support each half of the load and pretty soon the loading of the airplane started up uneventful. Several boxes of new cargo straps were used to secure that load to the airplane floor and once the crane crew and equipment was gone, the nose door closed, the crew luggage secured and the crew briefed on our charter for the day, we left Miami behind us for a short three hours flight to Omar Torrijos International, the Panama City airport ( as it was known at this time,after having been known as Tocumen International)
Tocumen International Airport was inaugurated on June 1, 1947 by President Enrique A. Jiménez, and airport operations began before the construction works were completed. The administrative building/passenger terminal was inaugurated seven years later, during the administration of Colonel Jose Antonio Remon Cantera.
The old airport building, which currently is being used as a cargo terminal, was built on an area of 720 ha (1,800 acres) and was 126 ft. (38 m) above sea level. As time passed, and due to Panama's role as a country of transit, that terminal became too small to attend to the growing demand for air operations. This compelled the aeronautical authorities at the time to consider expanding the airport. Work on the new buildings began in 1971.

(Manuel Noriega : the big boss in these days..He believed more in supporting narco-traffickers than in making investments in the Panama airport)
In order to build the structure that currently houses the current passenger terminal, a lot of land had to be moved and the bed of the Tocumen River had to be diverted from its original site. The current passenger terminal was inaugurated on August 15, 1978 and operations began on September 5 of the same year. The Tocumen International Airport is one of the few airports in the region that has two landing runways able to serve the largest commercial aircraft operating today.
The name of the airport was changed in 1981 by the military government for Omar Torrijos International Airport, in honour to the Panamanian leader who died in July 31, 1981, at the age of 52 in a plane crash in Cerro Marta, Coclesito in very bad conditions. After nine years, the original name was re-established after the fall of the dictatorship of Panama by the U.S. invasion of 1989.
The original runway (03L/21R) was mainly used for cargo and private flights, but also as a supplement to the primary runway during peak traffic periods. The main runway (03R/21L) was 3,050 m × 45 m (10,007 ft. × 148 ft.) and was used primarily for commercial flights, the 03R direction was ILSCat. I enabled.

(Offloading a "lengthy bit of cargo" from a Cargolux B 747 freighter)
Until May 31, 2003 Tocumen International Airport was managed by the Civil Aeronautics Directorate (which is known today as the Civil Aeronautics Authority). On June 1 of that year, an innovative terminal management platform was created through Law No. 23 of January 29, 2003, which set out a regulatory framework for the management of airports and landing strips in Panama. This law allowed the creation of Aeropuerto Internacional de Tocumen, S.A., also referred to as Tocumen, S.A., which currently manages the terminal. This law is one of a number of laws that restructured the aeronautical sector in Panama to further its improvement and modernization.
But in the middle of the 80’s, PANAMA was run by a ruthless dictator, Manuel NORIEGA, (later removed from office by the United States) who believed more in supporting “narco-traffickers” rather than civil aviation excepted when it was in his own interest. As a result, PANAMA airport was void of international standard equipment, under developed; giving the impression that clocks had stopped ticking at the end of the 50’s.

(The " new" buildings at Tocumen International)
At FTL there was no charter without a full charter briefing providing details about the crews, the flight schedules, and crew change points, details about the cargo load, handling agents, fuel supplier, overfly and landing rights, and other important information . The briefing specified that upon arrival in Panama City , the handling agent would provide us with the required handling equipment (GSE = Ground Service Equipment) in order to offload the airplane and be on our way back to Los Angeles, (while the sun would slowly disappear over the horizon and I would be drinking Pina Colada on my first class seat on the upper deck of our B 747-200).
This charter briefing represented the paper version of the ideal world and it is very interesting ( and I have verified this many, many times) to find out the difference of meaning for the same word in various countries and culture ! Asking for cleaning services in Harbin (Northern China) you would get a couple of young women clad in Mao blue or Mao green coming on board with makeshift brooms and dustpans, while in Paris, there would be a supervised team of seasoned airplane cleaners complete with electrical vacuum cleaners !

(Push back equipment . One end is connected to the push tractor, the other to the nose landing gear....)
Ordering catering in Frankfurt would see you through a couple of days, so rich was the food, while same order in India would include unknown although tasteful dishes and sauces accompanied by Nan bread, all of it packed in recycled cardboard boxes dripping with curry.
In the same fashion, expecting Handling equipment in Panama City to be the same as the one used the same morning in Miami was too farfetched and although I was now under and attack of anxiety when I saw what kind of equipment would be used, I had to accept that we had fallen into a trap and would not survive to the difference in technological level between that of glorious South America and that of Conquering United States !
In front of us, a few hundred yards of the airplane parking spot was an old US made crane, probably used in Panama Canal maintenance work… I say probably simply because when trying to document myself about this collectible, no one at the airport was able to tell me more about it, or about the kind of preventive or curative maintenance which had been conducted on the crane in the last 48 years.
I expected modern ground support, I ended up with ONE very old crane, a good will crane operator, four or five “ deck” hands and hope that I would not screw things up when conducting offload operation.
Rested, still fresh from a long morning shower in the hotel, Miami a short three hours flight time away, a lot of luck on my side, the offloading operation should go well. Why should I worry ?
I quickly donned my dark blue coverall patched with the Flying Tigers logo, the circle with the arrow, and proceeded to remove the 250 straps used to tie down the crankshaft. With the nose cargo door open, the straps removed, it was now time to slowly move the massive load towards its exit point. The B747-200 main deck was equipped with “smart wheels” systems technically known as PDU (power drive units) which could be remote controlled and turn forward or after as necessary, thus moving the ULD (Unit Load Device) along the floor of the airplane.

(Marshalling signals . Most of the airlines use these, the military may have other signals, some airlines have also developped their own for their own pilots...it can have a tricky result sometimes if a pilot does not know the internationally approved hand signals...)
In order to ease up the loading and of course the offloading, the 20 ft. pallets had been loaded as close as possible to the centreline of the main deck . No lateral movement would be required, or possible, during the transport of this cargo. Since no main deck loading plateform was available,(also known as MDL Main Deck Loader) the plan was to move the crankshaft resting on its cradle and on the pallets as far as possible, quarter or an inch by quarter of an inch, making sure that at least half of the weight would remain on the airplane. Once this would be done, and at least a part of the load cleared from the nose door thus allowing the crane to attach the sling on that load, I would reassess the situation and decide on the rest of the plan, which look minute by minute as if there was no plan at all !

(20 ft cargo pallets -20ft x 96 inches- use to carry havier-than-usual loads, or vehicules etc...these are mostly used for better spreading the cargo weight over the airplane structures, therefore reducing the "fatigue". Can be used in conjunction with heavy wooden shoring, straps, etc...)
When dealing with special loads of this type, anything that would be out of the standard operation, there was of course always a chance that thing would turn sour, and that the airplane may end up damaged. Our role was to ensure that this did not happen . Working by the book was nice, but our book was very thin, thus leaving a lot of space for “ operational creativity” to be use when getting out of difficult situations, and that was a part of the excitement about this job ! Was it luck or help by the loadmaster’s guardian angel, the heaviest part of the crankshaft seemed to be loaded towards the tail. There was no way to really assess what was exactly the weight spread and trusting my eyes and overall feeling was the best I could do.
Quarter of an inch by quarter of an inch…a quick push on the PDU joy stick from the master control station, ..the noise of the electrical motors driving the moving force ,the screech of hard rubber on the bottom of the pallets: the load was slowly progressing but how far could I get this shaft out of the nose without taking the risk of if tipping out of the airplane, tearing the upper deck, the cockpit ,making me the loadmaster who had lost of multi-million dollars airplane…?

( B 747 main landing gear...16 wheels....)
Working as a loadmaster is just like any other job. You need to have an open minded attitude, accept that you do not know everything, be glad when a more seasoned colleague shows you trade tricks, explains to you how to get out of dangerous situations, what to do and what NOT to do ( how to offload reluctant cattle from an airplane, how to open a “turnbuckle” without losing a finger, how to fuel a DC 8, how to conduct what was called “weight adjustments” when determining the weight of cows before preparing the weight and balance…) One of the charter representatives in our group told me one day :
“Use your brain, whatever math you may know, use it, always imagine that the aircraft belongs to you, and when things get difficult, stop work, go for a smoke and analyse your options”.. That day in Panama City was exactly the kind of day to put these recommendations in practice….
I had no knowledge about the crane lift capacity, but I decided to go down and see if I could get more technical information unfortunately after a short tour of this piece of machinery, my initial feeling was confirmed: I would manage only if I was lucky, the other option being to return the load in its initial positions, strap it down, ask “Ops Con” (our operation control office located at 7401 World Way West in Los Angeles),for a flight plan from Panama City back to Miami, fuel up and go, having forfeited my mission in the name of airplane an crew safety.
I did not like this kind of option ! By that time one of the adjustable cable of the sling was already tied around the part of the shaft that cleared the nose door but what was the cable strength ? Would the cable be strong enough ? I remember climbing on the half of the crankshaft still in the airplane, walking all the way to the other end, hanging over the parking and having the frightful vision of a steel cable, dry as a bone, an indication that the cable itself may have not been used in a long while, and possibly not to conduct this kind of operation… It was our airplane, our load,, why would the handling agent care ? Breaking the airplane would only end up in a legal dispute between our insurance company and the handling agent.
The end word would be that the loadmaster should have made the right decision, including that not to offload should he had estimated that all of the safety conditions were not met that very day.
I got scared and took the time, as I had been told to, to go for a smoke and think it over while the crew was in the terminal possibly looking for souvenirs at the duty-free shop. The clock was running, I was getting hot and tense.
Not so many planes parked around the terminal: it was a week day, and probably not the right period to go and visit Panama unless you would be a cocaïne addict .
The airport marshaller had parked us “ nose out”(*), parallel to and far enough from the airport building. I remember pulling my pack of cigarette, lighting one up just to pacify my body and give myself time for thoughts. Time was passing and pretty soon, crew duty time would become a real issue, regardless if decision was made to fly back to Miami with the cargo or, after possible offloading, fly back ferry to Los Angeles.
With half of the load outside of the airplane, the other half inside, the sling attached to the load, one idea came to my mind : ask the crane operator to lift the load by a few inches to take a look at the balance of the cargo. If indeed the sling had been positioned about half way of the crankshaft, and even if half of the load was still resting on the main deck at this time, this would give me a better idea of what the situation was, and we would then simply need to push the airplane back and clear the rest of the load. The crane would then lower the load onto the ground and this would made my day as my responsibility stopped as soon as the cargo was out of our control. 10 inches upwards was all that was needed to see if the load was balanced so the crane operator started applying tension on the cable and the load, incredibly, lifted up from the main deck and stopped in “mid-air”, totally clear from the airplane structure but one half still inside the airplane.
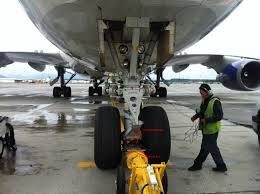
(When everything is standard, "brakes off", " ready to push")
Pushing back the airplane was now our best option to quickly finish the operation. This would take 15 minutes, crew would return from the terminal, load the INS up, we would fuel and go, and my Pina Colada was not so far away anymore. I asked the handling agent to position the push back tractor along with the tow bar…. There was no B747 tow bar There was no tractor able to push back a B747,even if empty There was just a sub-equipped South American airport … We were clearly F.....D !
Then I understood why they had parked us “nose out” !
I started wondering how long the cable would hold my load before it would simply snap, releasing 76.000 lbs on the main deck in a massive shock.We needed to find a way to push the airplane on about 5 meters to clear the load, close the nose door and get away from this horrible experience.
And then, an obvious detail struck my mind : on the main gear of the airplane there were only chocks preventing movement “after” and none preventing movement “forward” . Asking the ramp supervisor if we could get chocks for the front of the wheels, the answer he gave me came was both stunning and exciting…
“You have too many wheels, (18 in total) we do not have enough chocks. Don’t worry, the slope on the parking is not forward, it is back”…
The slope?
The wheels were chocked against the risk of the airplane slipping backward…! May be we had a solution there…
Through a quick briefing with the charter mechanic, it was decided that he would ride the brakes, we would remove the chocks, he would then release the brakes with the hope that the empty airplane would move back slowly . Using the ground to cockpit intercom equipped with a Clark headset, airplane surroundings being cleared of ground personnel, it was now or never .

(They pull forward, we pulled after...)
“Release the brakes ! “ I said And the answer came right back : “ brakes are released.” The airplane moves back two inches and stopped…our problem was not solved yet and after the brakes were set again, a new brainstorming took place .
“Why can’t’ we pull the airplane back ? “ I asked “First it is not in the procedures, then this airplane must be pushed from the front, and we don’t have a tow bar, we don’t have a push back tractor, and even if we have no fuel left on board the operating weight is still 170 tons…It would never work !! and on the top of that we need to get clearance from Maintenance Control and "Ops Con”
My Pina Colada was getting further and further away. Calling Los Angeles would take time, and we had none. Together we made the decision.
"Find ship rope, find people, many people, and at least try ! " This was the last chance we had and we knew that the parking slope was favourable ! Operating in a city with a harbour is a plus . Besides sailor’s bars and various nightly watering corners, there was plenty of ship’s tie down not far away, and two ropes of about 35 meters were found near what was called a “cargo terminal” looking like if it had been built in the time of the canal works ! Ropes were tied to a specific point around the main landing gears. I remember the mechanic making sure that they would not slip down by using metal sticking tape to maintain the rope on the main gears and rolling up cargo straps around the not to make sure it would hold.
A couple of hundred dollars changed hands and magically we found the right amount of workers. An interpreter was called to explain what was expected: 60 people on each rope, 24 people spread on the front part of the main landing wheels , the mechanic back in the skipper’s seat, this simply HAD to work !

(A Flying Tiger Line B 747)
I went back on the headset

“Check the brakes, confirm that brakes are set” I asked in the intercom “Brakes are set” came the answer” . 30 seconds for a quick brief, a thought for my guardian angels…
“When I tell you, you will release the brakes and confirm that brakes are released. The plan is to move the airplane back on about 5 meters and stop immediately once the load is cleared from the nose door. We know exactly where to stop”
“Tell me when you are ready” came the answer…
Marks had been placed on the ground using a spray of yellow paint conveniently borrowed from airport painters and I knew how far back we needed to more the plane. With all the key people at the right place, and hand signals agreed upon, the command was given, not knowing if this would work or not…
“Please ,release the brakes”… “Brakes are released, good luck”…
And the brakes were released and 144 people towed or pushed… then came the momentum as the airplane started moving very gently, inch by inch, by inch ,by inch….until the main gear wheels were on the yellow marker….
“Please set the brakes on, the load is clear from the nose door” “Brakes are set” came the voice
The right decision, at the right time, luck and slope did the rest for us and my Pina Colada was not so far away anymore…
When it is not in the books, always think outside the box…! And remember also that it is always easier to ask for forgiveness than permission.
© 2016 Sylvain Ubersfeld for Commercial Air Transport
(*) Unlike cars, most of airplanes do not have a real “reverse” capability. Depending on the airport installations, they are parked “nose in” in which case when ready to start they have to be “pushed back” using specific equipment. Parking an airplane “ nose out” means that the airplane will be able to leave its parking without a need to be “pushed back”. It is to be noted however that some types of aircraft , under specific circumstances , can move back using specific procedures, something that crews would rather not do unless strictly necessary.
Comentários